Unlocking the Potential of Corrugated Boxes in Modern Packaging
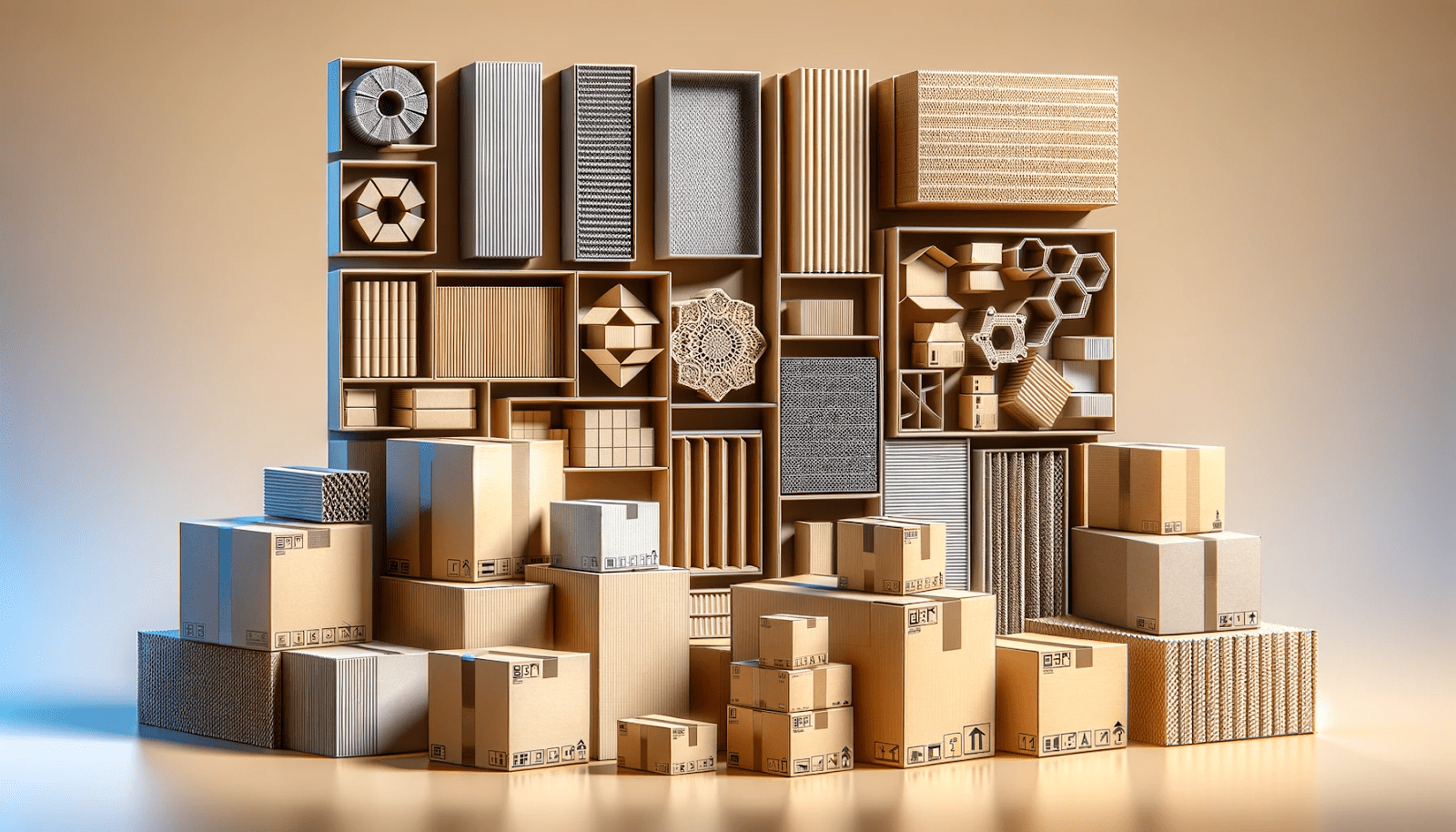
Welcome to the world of corrugated boxes, the unsung heroes of the packaging world! At Influence Packaging, we understand that a box is more than just a means to transport products; it’s a crucial part of your brand’s story. In this article, we’ll explore the versatility and importance of corrugated boxes in modern packaging.
What Are Corrugated Boxes?
Corrugated boxes are the backbone of the packaging industry. Known for their distinctive fluted, or corrugated, layer sandwiched between two sheets of paperboard, these boxes offer a unique combination of strength, durability, and lightweight design.
They are an eco-friendly choice, being recyclable and often made from recycled materials.
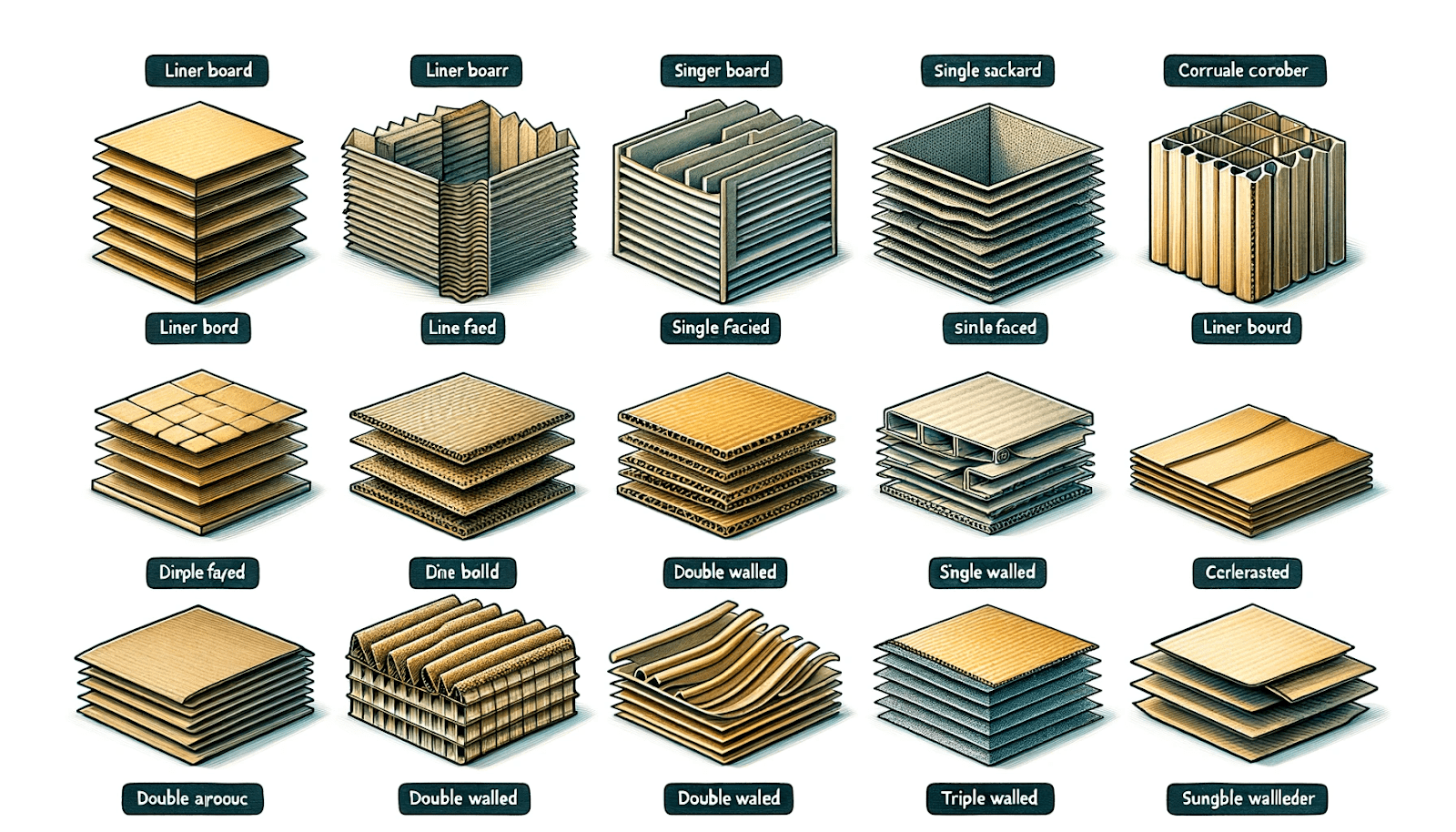
Types and Uses of Corrugated Boxes:
Corrugated boxes come in various types, each suited for different purposes:
Single-Faced: One sheet of liner is adhered to one sheet of corrugated medium. Ideal for wrapping products or as additional padding.
Single-Wall: The most common type, perfect for standard shipping boxes.
Double-Wall: Offers extra strength for heavier items or long-distance shipping.
Triple-Wall: The ultimate in strength, suitable for industrial parts or heavy machinery.
Each type serves a unique need, from lightweight, cost-effective solutions to heavy-duty packaging requirements.
Corrugated materials in Retail Store Displays:
In the retail world, the presentation of products can be just as important as the products themselves. Corrugated materials are not only pivotal in safely transporting goods; they also play a crucial role in effective retail store displays. Here’s how:
Customization and Branding: Corrugated displays offer immense flexibility in design. Brands can use this to their advantage by creating custom shapes, sizes, and printed designs that align with their branding. This customization transforms a simple corrugated material into a powerful marketing tool, one that speaks directly to the brand’s identity and values. Imagine a corrugated display that not only holds your products but also tells your brand’s story through vibrant colors, compelling graphics, and innovative design.
Durability and Versatility: One of the main strengths of corrugated material in retail settings is their durability. They can withstand the wear and tear of high-traffic retail environments, ensuring that products remain safe and displays stay intact. Additionally, their lightweight nature makes them easy to move and reposition, offering flexibility in retail layout and design. This versatility means corrugated displays can be used for a wide range of products, from lightweight items like cosmetics to heavier items like books or electronics.
Eco-Friendly Appeal: Today’s consumers are more environmentally conscious than ever before. Corrugated displays, being recyclable and often made from recycled materials, resonate with eco-friendly values. Retailers can leverage this to appeal to environmentally conscious customers, highlighting the sustainability of their displays and packaging choices. This not only elevates the brand’s image but also contributes positively to the environment.
Cost-Effective Solutions: Compared to other materials used for store displays, corrugated material is a cost-effective solution. This affordability allows businesses, especially small and medium-sized enterprises, to create attractive displays without a significant investment. It’s an efficient way to maximize the visual appeal and reach of products within a budget.
Enhancing Customer Experience: A well-designed corrugated display can significantly enhance the customer experience in a retail store. It helps in creating an engaging environment that can draw customers in and encourage them to interact with the products. This interaction often leads to increased sales and a stronger connection between the brand and the consumer.
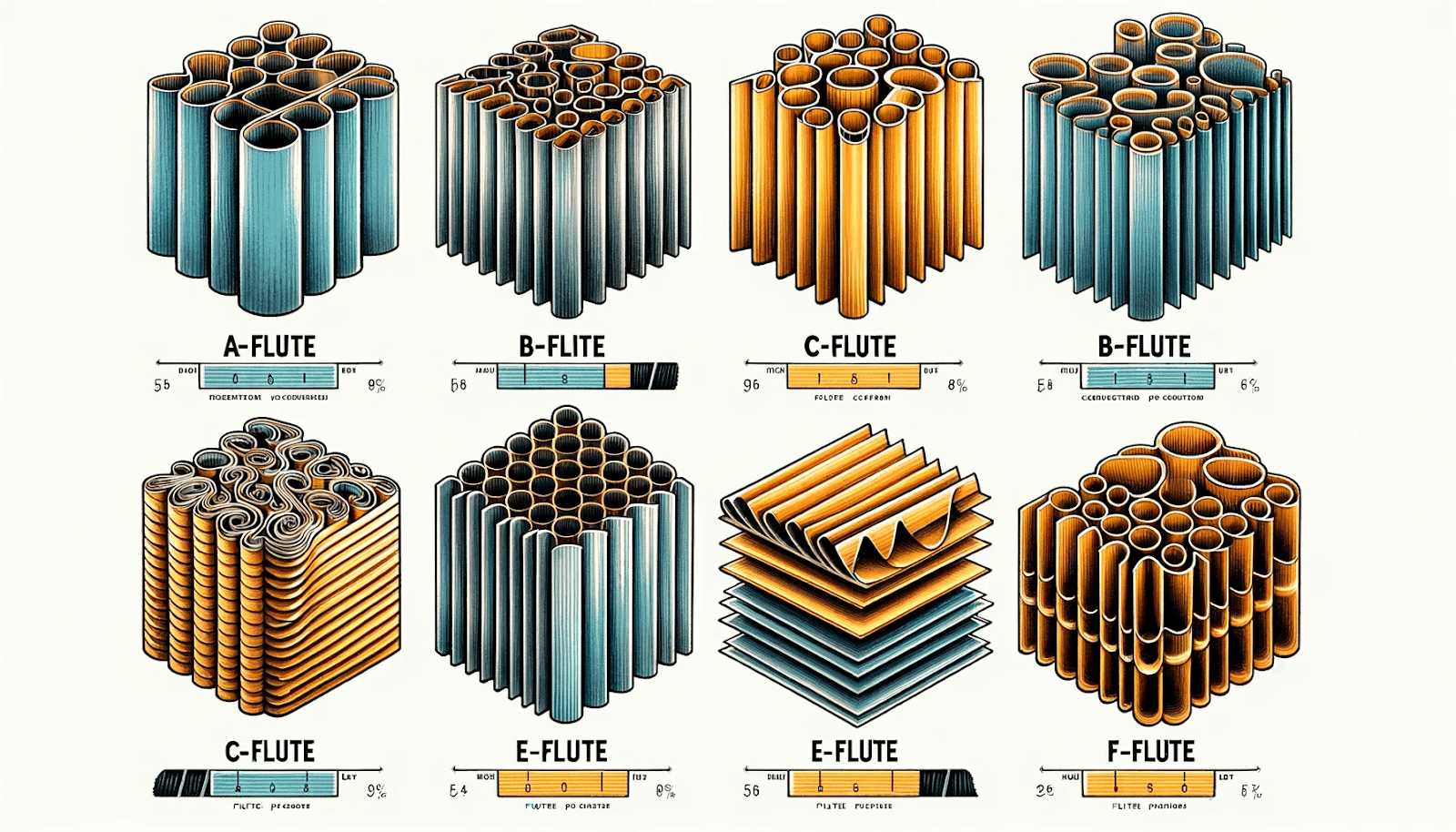
Corrugated Flute Grades: Understanding the Backbone of Corrugated Boxes
One of the key elements that define the strength and application of corrugated boxes is the corrugated flute grade. Flutes are the arches or waves found between the two liners in a piece of corrugated board. They not only provide strength but also play a vital role in protecting the contents and providing insulation. Understanding the different flute grades is essential in choosing the right type of corrugated box for your specific needs.
A-Flute: This is the original flute grade for corrugated boxes and is the thickest. With about 33 flutes per foot, A-Flute provides excellent cushioning and stacking properties. It’s perfect for fragile items and for boxes that require more strength for stacking.
B-Flute: More refined than A-Flute, B-Flute has a higher flute count at about 47 flutes per foot. This grade offers a good balance between protection, box strength, and flat surface suitable for printing. It’s commonly used for die-cut boxes and for packaging consumer goods.
C-Flute: Falling between A and B, with around 41 flutes per foot, C-Flute is often chosen for shipping cases. It offers good cushioning, stacking, and printing properties. Its versatility makes it popular for a wide range of products.
E-Flute: E-Flute is thinner with around 90 flutes per foot, offering excellent crush resistance and a relatively flat surface suitable for high-quality printing applications. It’s commonly used in retail packaging and is great for delicate items.
F-Flute: The thinnest at about 128 flutes per foot, F-Flute provides a very smooth surface for high-quality printing and is often used for specialty packaging and retail displays.
Micro-Flutes: These are the newer types of flutes that are thinner and more eco-friendly. They are becoming increasingly popular due to their reduced material usage and lighter weight, which helps in reducing shipping costs and environmental impact.
Each flute grade has its unique characteristics and uses. The choice of flute grade affects the box’s performance in terms of strength, printability, and protectiveness. Understanding these grades helps businesses select the right type of corrugated packaging for their products, ensuring optimal protection, while also considering cost-efficiency and sustainability.
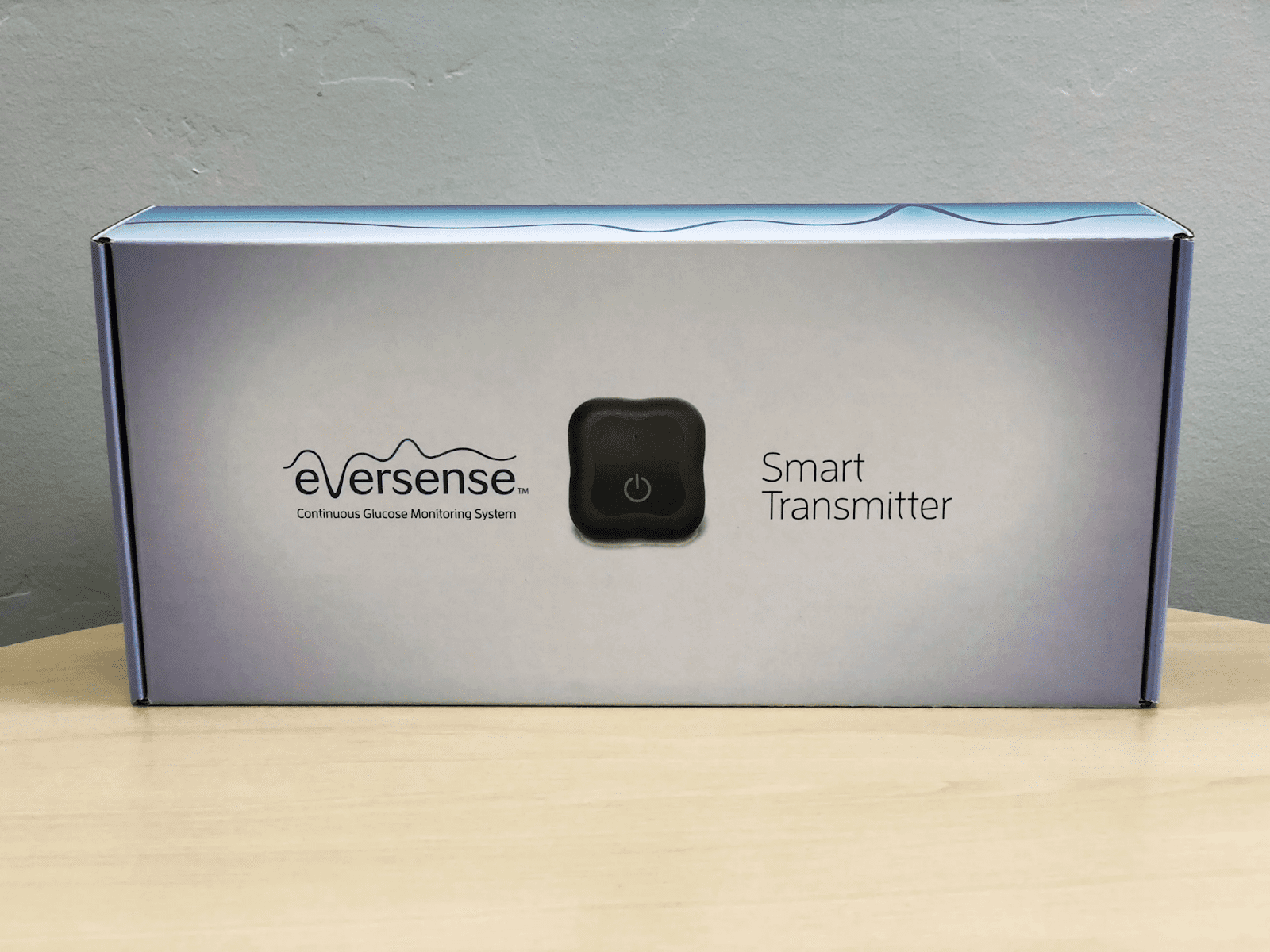
Exploring the Diversity of Corrugated Box Styles
Corrugated boxes are not just about strength and durability; they also come in a variety of styles, each designed to meet specific packaging needs. Understanding these styles is crucial for businesses to select the right packaging solution that combines functionality, efficiency, and aesthetic appeal. Let’s explore some of the most common corrugated box styles:
Regular Slotted Container (RSC): The most standard and widely used corrugated box style. All flaps have the same length, and the two outer flaps (usually the longer pair) are one-half the container’s width, so they meet at the center when folded. This design is efficient, cost-effective, and suitable for a wide range of products.
Half Slotted Container (HSC): Similar to the RSC but without one set of flaps. This style is often used for products that require a top-open box, like large and bulky items.
Full Overlap (FOL): The flaps on this style extend all the way to the opposite side of the box, providing extra strength and durability. This makes it ideal for heavy or fragile items that require additional support.
One Piece Folder (OPF): Made from a single piece of corrugated board, this style is typically used for flat items like books or picture frames. The box wraps around the product, providing a snug fit and excellent protection.
Telescope Box: This style consists of a separate top, or lid, that fits over a bottom piece. It’s great for products that need to be frequently opened and closed, like board games or shoe boxes.
Die-Cut Boxes: Custom designed and manufactured with a cutting die. These boxes can be made in virtually any shape and size, offering a high degree of customization for specific product needs, often used for retail packaging.
Mailer Boxes: Commonly used for e-commerce and subscription boxes, mailer boxes are easy to open and typically don’t require additional tape. They are ideal for delivering products directly to customers.
Each corrugated box style has its unique advantages, from the cost-effective simplicity of RSCs to the tailored, brand-enhancing appeal of die-cut boxes. By selecting the appropriate style, businesses can ensure their products are not only well-protected but also presented in a way that enhances the customer experience.
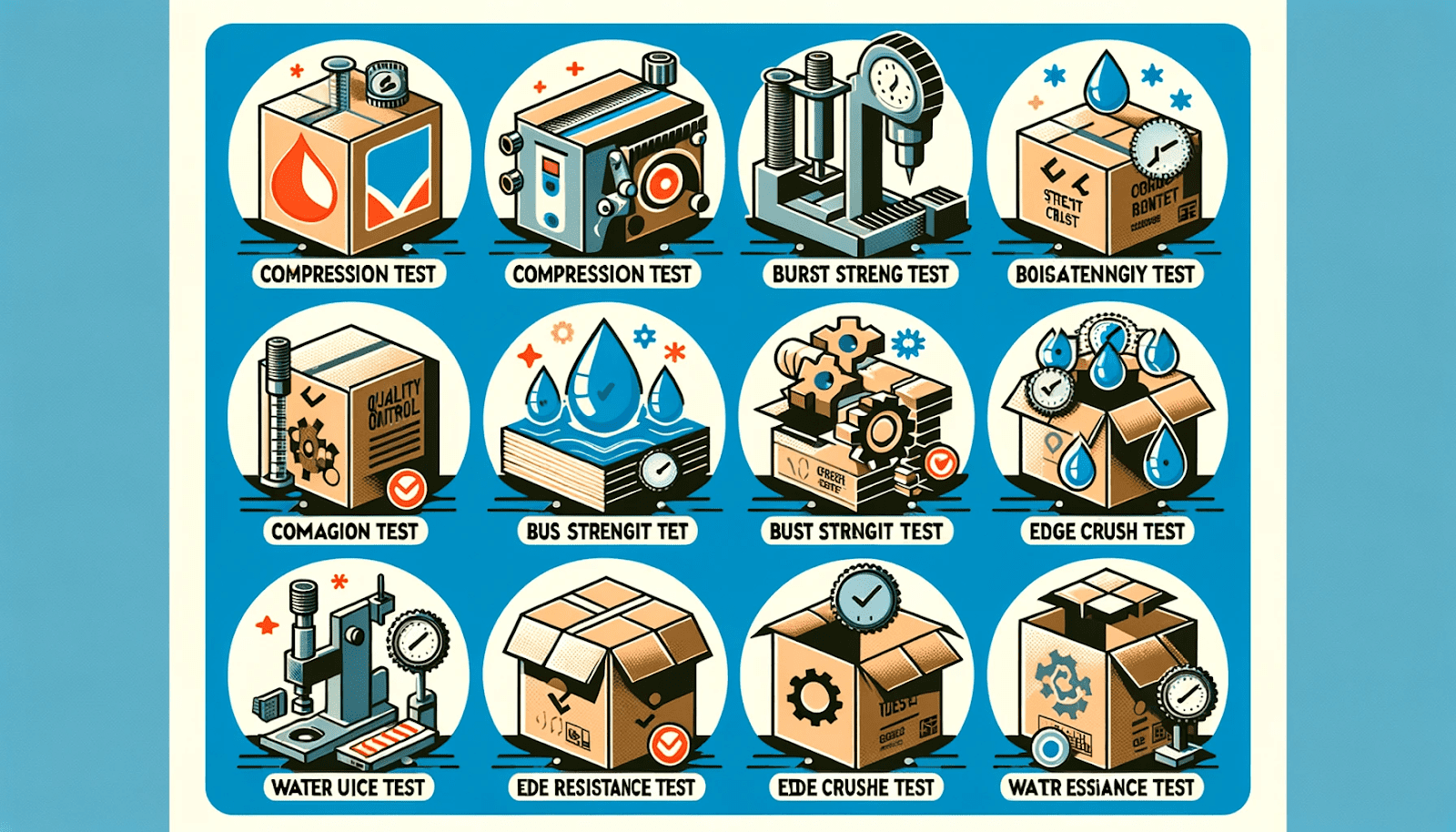
Quality Control Tests for Corrugated Boxes
When it comes to corrugated boxes, ensuring their quality and durability is crucial, especially since they play a vital role in protecting products during transport and storage. Quality control tests are designed to assess the performance and reliability of these boxes under various conditions. Let’s delve into some of the key tests conducted:
- Edge Crush Test (ECT)
The Edge Crush Test measures the stacking strength of corrugated board. It helps determine how much weight a box can withstand before collapsing. This test is essential for manufacturers to ensure that their boxes can handle the rigors of stacking during storage and transit.
- Burst Strength Test
This test evaluates the ability of the box material to withstand pressure from within, simulating the forces the box may encounter during shipping. It’s particularly important for boxes carrying heavy or unevenly distributed items.
- Water Absorption Test (Cobb Test)
The Cobb Test measures how much moisture the corrugated material can absorb over a specific period. This test is crucial for products that require protection from humidity or will be stored in moist environments.
- Box Compression Test (BCT)
BCT assesses the load-bearing capacity of a box. It is vital for understanding how much weight the box can handle before it deforms or collapses, ensuring the safety of the contents during shipping and handling.
- Puncture Resistance Test
This test determines the durability of the corrugated board against punctures or tears, which is essential for protecting products from sharp objects or rough handling.
- Peel Adhesion Test
The Peel Adhesion Test measures the strength of the adhesive bond between the layers of corrugated board. A strong bond is crucial to maintain the box’s structural integrity.
By conducting these tests, manufacturers can assure the quality and suitability of their corrugated boxes for various applications, ensuring that they meet industry standards and customer expectations. At Influence Packaging, we rigorously test our products to guarantee their performance, offering you the best packaging solutions for your needs.
Are Custom Corrugated Boxes Right for You?
Are custom corrugated boxes the right choice for your business? The answer lies in understanding your specific needs and goals.
Custom corrugated boxes offer a plethora of benefits, from enhanced brand recognition to precise product protection. They allow you to tailor the size, shape, and design to match your product’s unique requirements, ensuring an ideal fit and optimal protection. Moreover, the ability to incorporate your brand elements – like logos, colors, and messaging – can significantly boost your marketing efforts, making your packaging a silent yet powerful ambassador of your brand.
In summary, custom corrugated boxes are an excellent choice if you’re looking to elevate your brand’s presence in the marketplace and provide a memorable unboxing experience for your customers, all while ensuring your products are well-protected. At Influence Packaging, our team of industry experts will walk you through the production requirements, operational requirements and ensure you deliver the highest quality products on time to your customers.
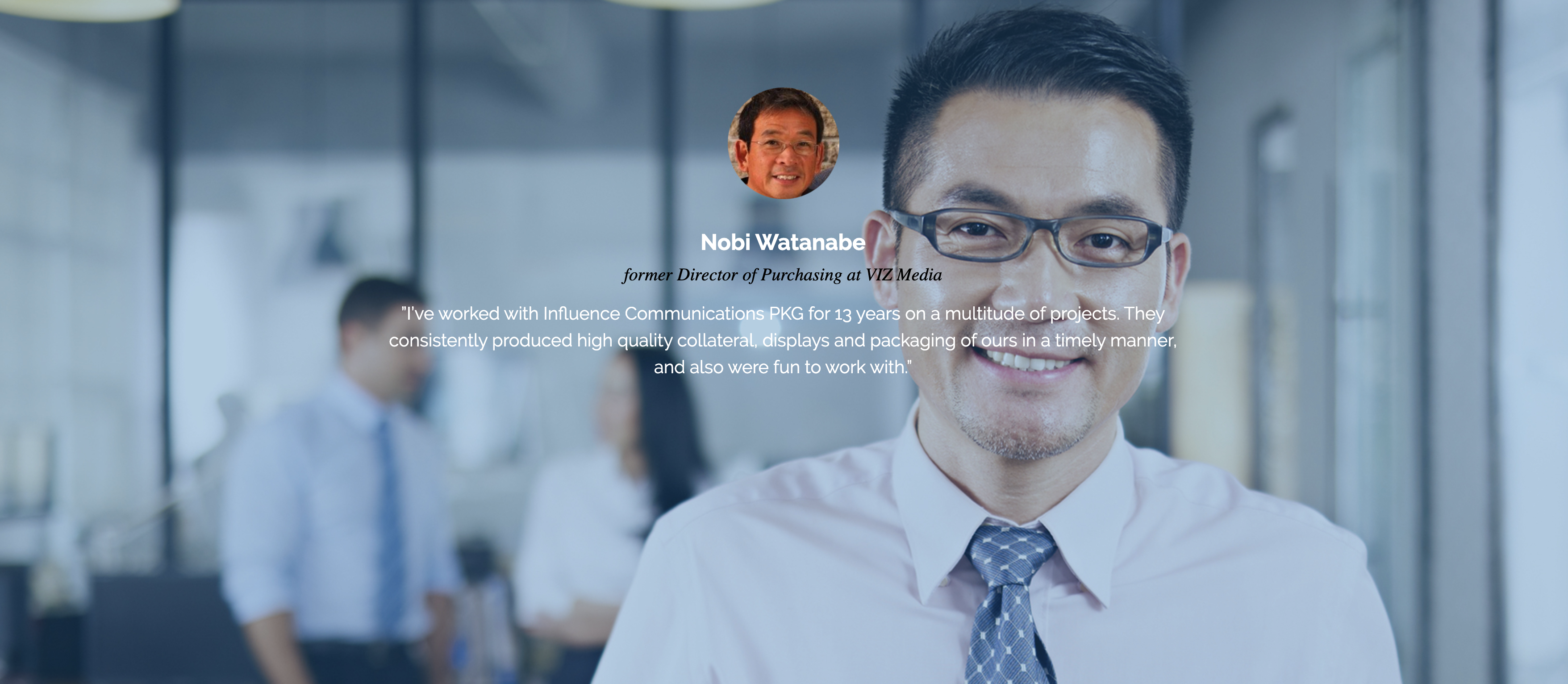

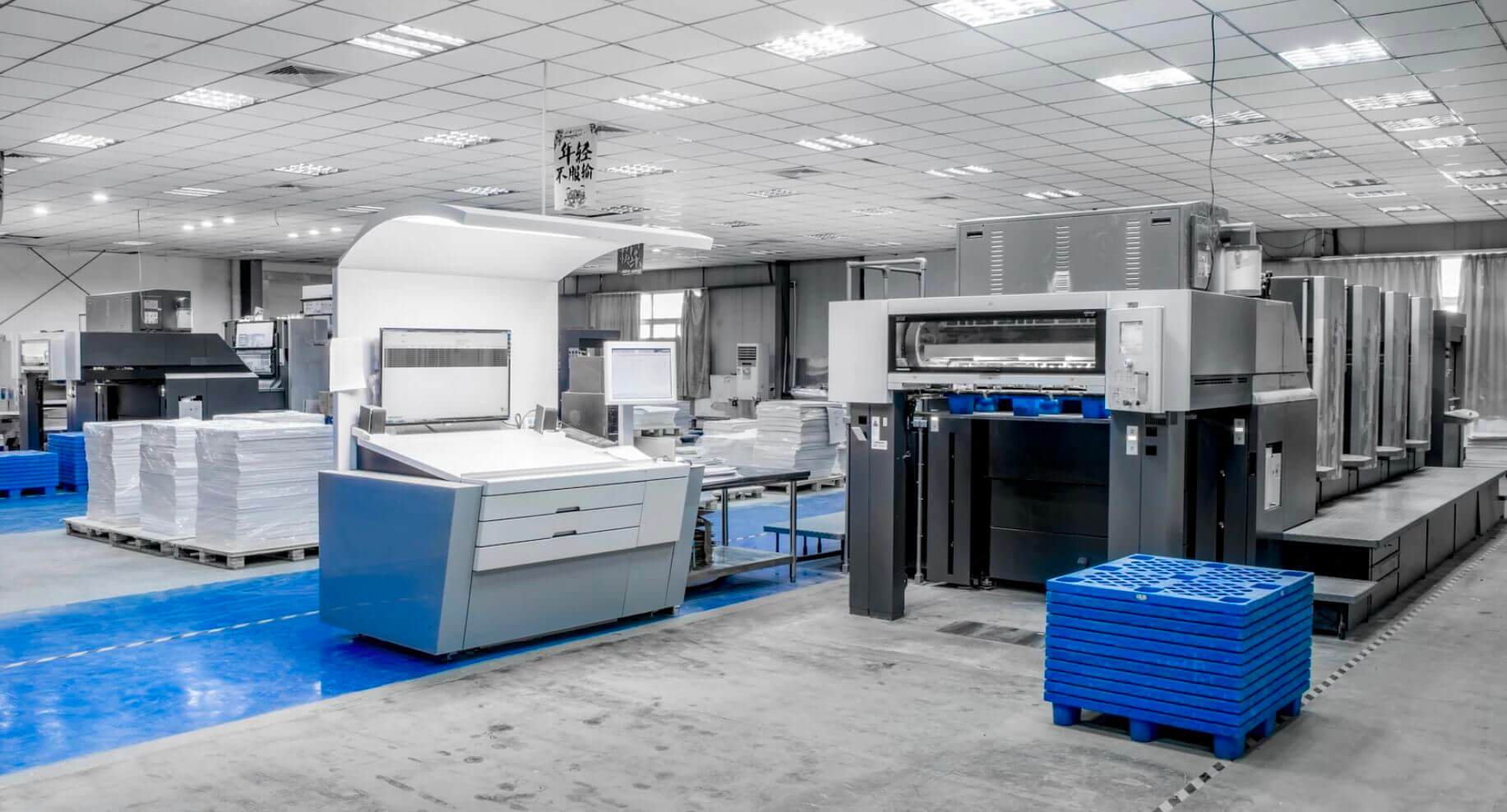
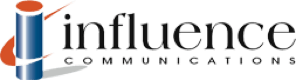
Influence Packaging is an award winning Custom Box Packaging Company leading the best packaging projects since 1994.
We are headquartered in Oakland (San Francisco Bay Area), California and we can’t wait to hear about your next packaging project!
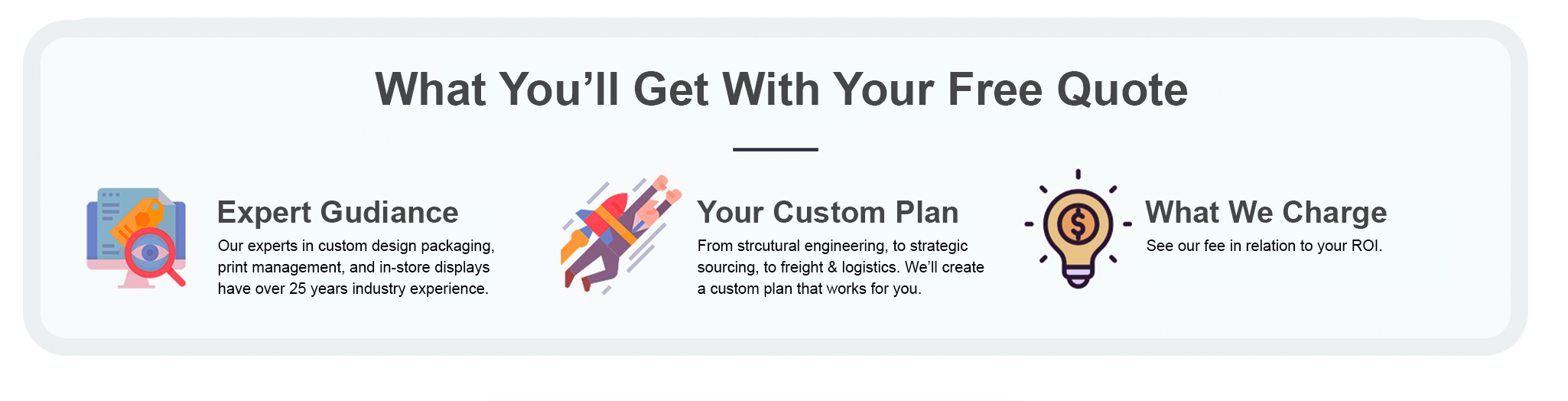